Plans Can Change
Boeing Rips Page out of Airbus' BookPlan backwards as well as forward. Set objectives and trace back to see how to achieve them. - Donald Rumsfeld When defeat comes, accept it as a signal that your plans are not sound, - Napoleon Hill Passenger capacity 200, non-stop flight distance 7,595 miles, cruising speed 627 miles per hour, by Byron Acohido Seattle - Is Boeing morphing into Airbus? By turning to contractors in several countries to supply most of its newest jetliner model - including the wings - Boeing not only breaks with tradition but apes a strategy its rival, Airbus, has used for years. Even the method that Boeing has chosen to bring the large sections of its proposed 7E7 to the US for assembly is a bow to Airbus, a consortium of European aerospace companies that this year will take more orders and deliver more commercial jets than Boeing. Boeing says it will modify at least three 747-400 jumbo jets to air-ship the large parts, imitating Airbus' use of a bulked-up A300-600 jet - nicknamed Beluga - to shuttle airplane sections between factories in Germany, France, the United Kingdom and Italy. Boeing now relies mainly on ships, rail cars and trucks for transporting airplane parts to its assembly plants in Washington and California. By adding air freight - handled by what looks like a 747 on steroids - Boeing hopes to push more detailed work to key partners, much like Airbus does with its members. "This isn't your father's Boeing anymore," says aviation industry consultant Scott Hamilton. Boeing is following Airbus' lead more and more these days." Boeing is pointing toward a decision, perhaps in the next few weeks, on where the 7E7 will be assembled. Company directors are expected to formally green-light the model by 31 December, putting the first delivery in 2008. More than a dozen cities and states offered incentive packages to land the 7E7 plant, led by Washington state's offer of $3.2 billion in regulatory and tax concessions. Whoever gets the plant will reap only 1,200 new factory jobs, a far cry from the 10,000 workers Boeing needed in the 1980s to produce a 747 every 23 days. While the airliner project itself is tentative, planning for 7E7s manufacture is well along. Earlier this month, Boeing announced the formation of a "7E7 Council," composed of senior executives from six outside suppliers, plus Boeing divisions in Wichita and Tacoma, Washington. The council will act as the 7E7s contracting hub. Instead of dealing with Boeing headquarters, thousands of suppliers will work through the council members, each of whom will become responsible for delivering largely completed airplane sections. Cutting costs and timeCompare the 7E7 (above) with Boeing's 767-300-ER and Airbus' A330-200. Boeing's goal is to pare costs and reduce assembly time. Using Japanese-style just-in-time inventory techniques, it wants to roll a new 200- to 250-seat 7E7 out the factory door every three days, instead of every 12 to 17 days as it now does with its other models. "We're really trying to integrate our partners into this process, so they can optimise the production sequence ... in order to drive the most efficient production system up and down the supply chain," says Mike Bair, senior vice president of the 7E7 program. A confluence of forces is driving Boeing to change the way it builds airplanes, including:
Suppliers gain authorityBoeing plans to rely on suppliers to a greater degree than ever to build its proposed 7E7 model. That means thousands of Boeing suppliers will have to figure out how to pitch their goods and services to Boeing's prime partners, who may be located in a different state or overseas, says john VickIund, president of a not-for-profit consulting firm, Washington Manufacturing Services. "This is happening everywhere in manufacturing: in electronics, wood products, textiles, you name it," Vicklund says. "As a smaller shop, you don't have to roll over and play dead. It depends on whether you're willing to change your way of doing things." Some critics say Boeing's rush to offload key jobs to outside suppliers is shortsighted. For its entire history, Boeing has jealously guarded its techniques for manufacturing airplane wings. Now Mitsubishi Heavy Industries of Japan is making a strong bid to manufacture the 7E7's wing in Japan. "In the end, if we teach everybody how to make the major parts, why is Boeing even needed?" asks Jennifer MacKay, president of the Society of Professional Engineering Employees in Aerospace, the union that represents Boeing engineers and technical workers. "Having a viable workforce is what put Boeing where it is today, yet this is the very thing they're cutting." A model of the 747-400 freighter, with its forward hump widened and extended the length of the fuselage, underscores how Boeing is positioning itself to let Japan supply the 7E7's wing. The freighter appears to have room to accommodate the 7E7's 21-foot-wide fuselage sections and 85-foot wing sections. By cutting shipping time from a month by sea to less than a day by air, Boeing estimates it could save up to 40% in shipping and inventory expenses. But it still wants access to a shipping port. "If something were to happen, and we had to go to a backup plan, and we didn't have water access of some kind, we would have no way to get parts to final assembly," Blair says. Source: USA Today Wednesday 22 October 2003; top sketch is an artist's rendering courtesy Boeing, bottom two illustrations by Robert W Ahrens, USA Today from Boeing, Airbus and USA Today sources Et VoilàAirbus is to unveil three new planes. Its battle with Boeing has never been more intense. It is always the way with Airbuses: you wait for years, and then three come along at once. In January, the European aircraft manufacturer will roll out the first of its A380 super-jumbos, in preparation for its first test flight by the end of March. Before that, however, it is set to unveil plans for two versions of a smaller, wide-bodied plane, aimed at the mid-sized market. The rivalry between Boeing and Airbus, the big commercial-aircraft duopoly, has never been more intense. While Boeing struggles to persuade mainstream airlines to buy its latest offering, the 250-seater 7E7, Airbus will soon announce two versions of a new plane, dubbed the A350, to attack it head on. Boeing has high hopes for the 7E7, its first new model in over 10 years - after the flop of two earlier proposed products, a near-sonic widebody and a radical upgrade of the venerable 747, which did not find favour with airlines. Adding to its woes, the cancellation this week of a US Air Force order for refuelling tankers means Boeing will soon have to shut the production line making its 767 ageing widebody jet. On November 29th, the board of the parent company of Airbus, European Aeronautic Defence and Space company (EADS), meets to rubber-stamp a decision to launch two souped-up versions of its A330, fitted with new wings and engines to increase the range and carrying capacity and so compete with Boeing’s plane. Boeing’s new design claims to offer savings of 15 - 20% on fuel by making extensive use of lightweight composite materials instead of the usual aluminium. Anticipating Airbus’s response, last month Boeing persuaded the American government to complain to the World Trade Organisation (WTO) about the subsidies Airbus receives from European governments. Refundable launch aid from Germany, France, Britain and Spain could cover 1/3 of the over €3 billion cost of developing the A350. Crucially, this aid does not have to be repaid if a plane flops, giving Airbus an unfair advantage in product development, which it has ruthlessly exploited in the past decade. Boeing is spending almost $6 billion to develop the 7E7, with further contributions from its partners in Japan and Italy. The European Union is counter-protesting to the WTO that Boeing gets all sorts of indirect aid from the American government. The likeliest result is that both sides are found guilty of breaking the rules but that subsidy continues to flow. That is what happened in a similar dispute at the WTO between Canada and Brazil, whose two manufacturers share the market for smaller (up to 100 seats) jet aircraft. Meanwhile, flushed with his recent success in the market, Airbus’s chief executive, Noel Forgeard, is blatantly lobbying for the top job at EADS, now shared by a Frenchman and a German under a deal due for review by next June. He is talking up the desirability of EADS buying Thales, a French defence electronics company. That appeals to the French government, but may upset the Germans, who see it as a plot to make EADS a thoroughly French company, with the Germans sidelined. Source: www.economist.com 25 November 2004 Another Example of Plans that ChangeSource: British Airways advertisement For a photograph of a jet taken just as it achieved the speed of sound (and also a temperamental video clip, see also:
US Air Traffic During a Single Day(Flash plugin required)
Click to Begin (slight delay at the beginning) Desperately Seeking LightnessComposites: As they struggle for market leadership, Boeing and Airbus Since Boeing acquired McDonnell Douglas in the mid-1990S, there have been only two aircraft companies (Europe's Airbus Industrie being the other) that are capable of building commercial jets with more than 100 seats. Over the next 20 years, the market for such aircraft is expected to be at least $1.2 trillion. Which of the two will take the bigger slice of that market? There are few engineering tricks left that could give one or other a technological edge. There is little to choose in terms of the aerodynamic efficiency of their designs. The engines they use are identical. The latest version of either company's aircraft is only a few percentage points better than its predecessor. Long gone are the days when Boeing's 747 jumbos almost quadrupled the productivity of the Boeing 707S and Douglas DC 8s that they replaced, or the earlier doubling of productivity that those airliners made over piston-engined planes. On top of that, customer finance is more or less equal. Government agreements now prevent flagrant subsidies on both sides of the Atlantic. Of course, the American and European governments still underwrite much of the research and development that underpins their respective aircraft industries. Even so, none of this has moderated the price war between the two companies. It used to be argued that, once there was a clear duopoly in civil-aircraft manufacturing, aircraft prices would rise. That theory has been thoroughly discredited. The best indicator of new-aircraft prices - the average price per seat, adjusted for inflation - has been declining for several years, thanks to brutal competition between the two rivals. According to Airline Monitor, the cost per seat declined by 11% in real terms from 1995 to 2001, even though there was a booming demand for new aircraft. That leaves only aircraft weight (and its close cousin, manufacturing cost) as the key area in which the two makers can innovate. Airbus is pressing ahead with the use of composites in its new A380, the 550-seat behemoth that is now in full development and should come into service in 2005. Jens Hinrichsen, the director of structures at Airbus's large aircraft division, claims that, as the design now stands, around 40 tonnes (18%) of the A380'S structural weight will consist of carbon fibre. Airbus's efforts are being encouraged by the European Union. Under the EU'S Fifth Framework programme, aeronautical research was allocated $630m for a five-year period ending this year. This programme includes the so-called Tango projects for encouraging the use of composite materials in civil aircraft, with the aim of cutting 20% from both the weight and the manufacturing cost of new European airliners. If that order of saving were achieved, it would be equivalent to an 8% reduction in direct operating cost. Tango is split into four main projects: an all-composite wing, plus the structure where it joins the fuselage; two rival fuselage programmes (composite versus metal); and a composite centre-section box that joins the two wings at the base of the fuselage. The projects are clearly designed to support Airbus's upcoming P322 programme, a 110- to 180-seat design intended to replace the Airbus A320 family. The P322 is to be launched later this decade. But already, work on one particular Tango element - the centre-section wing box - has been accelerated so it can be used on the A380. Altogether, $38m of Fifth Framework money is being spent on composite applications, plus an equal amount from the 35 companies participating in the research programme. If that sounds like a backdoor subsidy, it is. And Europe's increase in taxpayer support for aeronautical research is happening just as American taxpayers' support for aeronautics and composites research by their own aerospace agency, NASA, is in decline. It is no secret that the EU intends to use these programmes to help Europe gain the lion's share of the large commercial-aircraft market. Shedding weight is crucial. For one thing, the heavier the structure the larger the engines needed to push it (and the extra fuel that is needed} through the sky. In turn, that means that less payload - passengers and freight - can be carried. Reducing the A380's structural weight by eight tonnes (around 3% of its weight} would cut 2% from direct operating costs - and on such differences are sales made. A lighter plane is also quieter. That is because less power is required, and there is a smaller mass carving its way through the air. This second point is important when it comes to landing noise, since a lighter plane needs fewer noise-creating flaps and other devices to help it to slow down when landing. Moreover, a lighter plane is cheaper to make, since it requires less of the expensive materials that are used in aircraft manufacture. Composites offer designers a way to lose weight, thanks to their better mechanical properties. But costly composites cannot be justified throughout an aircraft. For instance, an earlier version of the A380 design planned to use composites for the outer wing section, while retaining a conventional aluminium structure for the inner section. This idea was dropped for two reasons. First, given today's composite technology, it was hard to beat the cost of an aluminium wing. Second, the heavy joint needed to ensure that the loads between the two parts of the wing were transferred properly meant that there was no significant saving in weight. Apart from all the carbon fibre going into the A380, another 4% of the aircraft will be made of a new hybrid composite material called Glare. This is a sort of multi-layered sandwich made of sheets of aluminium foil interleaved with carbon fibre. When it designed the 777 in the early 1990s, Boeing rejected Glare because it was untried at the time. But since then, Glare has proved itself amply. At Airbus, the use of Glare in the A380 fuselage will save 7% of the weight of the metal parts it replaces. It will also mean a much better fatigue performance (resistance to cracking caused by repeated flexing). The chart below shows where composite materials are to be used in the A380. What is clear is that composites have overcome doubts about the size of parts they are good for. The rear of the plane is a good example. The A380's pressure dome - a 16-metre high bulkhead at the back of the double-decked cabin - is to be made by automatically laying fibres into moulds, a process well suited to structures involving double curvatures. The composite material for the job costs $115-125 a kilogram, compared with $20-30 a kilogram for the aluminium it replaces. But aluminium would require many panels, and the stretch-forming process used to make these involves a huge waste of material. The reduction in the number of panels also cuts assembly costs - in labour as well as in expensive fasteners. Better still, there is a 10% saving in weight. The unpressurised section of the rear fuselage, between this bulkhead and the tail, may also be partly composite. Massive metal forgings and frames will be needed to carry the aerodynamic loads of the tail surfaces, but the skin and the rest of the structure (56% of its weight) will be made of carbon fibre. Instead of the 16 aluminium panels that are needed in a conventional metal design, there will be four composite panels, making a net weight saving of 12%. Airbus engineers expect a further 4% saving in the cost of assembling this section of the aircraft. One of the biggest lessons that Airbus engineers have learnt is that the greatest savings accrue when the design of a part is not simply replicated in "black metal" (a reference to the shiny black colour of carbon fibre). The real pay-off is when the design is rethought to take full advantage of the composite's properties - and not just its strength-to-weight superiority. For instance, by careful design, components built out of a composite material can be made in a single, accurate piece, eliminating costly rework as well as heavy bolts and rivets. That means external surfaces can be a good deal smoother, reducing aerodynamic drag, and saving both fuel and further weight. Several different manufacturing methods are being used for the composites on the A380. There are still a large number of parts in which the composite - mostly in the form of sheets and tapes of carbon fibres pre-impregnated ("pre-preg") with resin - is laid into moulds by hand. The size of the parts made by hand is limited, because of the difficulty in aligning the fibres accurately over large sections. As a resuit, hand-layup tends to be used for making one-off prototypes or for less critical parts of an aircraft, such as "fairings" that simply smooth the airflow. To save labour and produce composite parts with greater consistency, aircraft manufacturers are learning to automate their production processes. For instance, the floor beams for the A380's upper deck are to be made in Japan using a continuous process akin to extrusion. In "automated tape laying", pre-preg tape is wound into a mould or on to a mandrel. That works well for simple shapes such as circular tubes or box-sections. But for more complex shapes, a process known as "automated fibre placement" has to be used to wind the pre-impregnated fibre precisely around the component's intricate contours. The result is very accurate, high quality parts - but at a price. Some of these parts require double-sided moulds. And all of them have to be placed in a vacuum bag - to squeeze the air out of the resin and ensure good bonding - and then cured at temperatures of up to 200°C in a costly oven called an autoclave. To complicate matters even further, pre-preg composites have to be kept refrigerated up to the moment that they are wound on to a mould, in order to prevent the resin from beginning to cure. Hence the trend towards so-called "resin infusion". This uses a single-sided mould into which dry fibre is placed. This material is then stitched together using techniques borrowed from the textile industry. Parts made in this way can be extremely complex. The "ribs" and "stringers" that form the inner structure of a wing can be sewn into place, with the fibres aligned precisely to gain the maximum strength. When the resin that bonds the fibres into a composite is injected, a complete part is made in one shot. This technique was demonstrated (on a Boeing 737-size wing) by NASA engineers as part of a $300 million programme that ran for 10 years until 2000. One novel technique that has caused a stir among aircraft engineers is a process developed by Quickstep Technologies of Perth, Australia. This uses a bath of heated water or oil instead of an autoclave to do the curing. The component being fabricated is enclosed in a vacuum bag and the internal pressure is then reduced moderately. The bag is dunked in the bath of heated liquid, which is then vibrated to ensure that all the air is shaken out of the resin so that a good bond can be made. Quickstep claims that this produces high-quality parts at a much lower cost. A different approach to cutting costs is being taken by GKN, a British engineering company. One of GKN'S American subsidiaries is applying basic production-engineering know-how to making composite parts. It groups machines into "manufacturing cells" to get better throughput, and uses automated multi-axis machines to lay fibre, trim parts after moulding, drill holes and so on. Composite technology today is where aircraft alloys were in the 1960s. Progress with the material is making rapid strides, but supplies are still limited. And the suppliers themselves are small, undercapitalised and due for a shake-out. No fewer than 800 suppliers from around the world had stands at a recent exhibition in Paris. The American Department of Energy reckons that the world market for aviation-quality carbon fibre is around 6,800 tonnes a year, with 60% of that going for military use. A quarter of America's F-22 fighter is made of fibre and over a third of the new Joint Strike Fighter will be made of composite. Even at a low production rate of two aircraft a month, the A380 will require a further 960 tonnes a year. Some industry insiders worry that this sudden increase in demand could outstrip supply. What will happen, they ask, if one of the large car makers comes out with a popular sports car made of high-grade carbon fibre - along the lines of the Lotus Elise? Composites face other challenges as well. The metals producers are not standing still. Laser-welding and other fabrication processes are now being used to reduce weight and assembly cost. That alone probably makes an all-composite commercial airliner unlikely. Another problem for composites is how to repair them. Airlines need to have handy repair methods - akin to riveting patches over damaged parts - so that they can get damaged aircraft back in service quickly. There are also questions over how to detect potential weaknesses in composites, following the failure of the composite fin on an American Airlines A300 that crashed in New York in 2001. For the time being, Airbus is ahead in using composites in commercial airliners. It has a record of being more aggressive than Boeing in adopting new technology. But, then, so did McDonnell Douglas - although its demise had more to do with low overall investment than taking technological gambles. The question now is whether Airbus's technological assertiveness will win it the lion's share of that $1.2 trillion feast. One thing is clear, however: ensuring that it does is now official policy in Brussels. Source: The Economist Technology Quarterly 21 September 2002 To view other articles related to flying including history, unusual flying machines, hot air balloons, skydiving, gliding, problems, airports, turbulence, pilots, crashes, the
Paris Air Show, the future, blimps, space travel, solar sails and more, clicking the "Up" button below takes you to the Table of Contents for this section on Flight. |
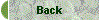
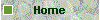
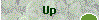
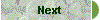